Efficiency Spotlight with Vertical Harvest Farms
By collecting data on resource use, like annual energy consumption (electric and non-electric), along with crop production, Vertical Harvest established baselines to compare against year-over-year. With these datasets, the team can identify, quantify, and validate energy savings strategies.
Jackson Hole, Wyoming, is unable to produce food year-round through traditional outdoor agriculture due to seasonal freezing temperatures. Vertical Harvest Farms has taken on the task of meeting its community’s need for fresh and healthy food by producing crops in its hydroponic farm.
Vertical Harvest grows leafy greens, herbs, and tomatoes in a state-of-the-art greenhouse facility, delivering fresh produce to local partners. “Local production and delivery is at the heart of our organization,” says Nona Yehia, Vertical Harvest’s co-founder and CEO. “We prioritize selling 75% of our produce within 150 miles of our farms before we tap into wider distribution networks to ensure food grown here stays here.”
At Vertical Harvest, community engagement goes beyond providing fresh produce. For example, Vertical Harvest’s workforce program provides meaningful work and upwardly mobile career opportunities to employees with developmental, intellectual, and physical disabilities.
Today, Vertical Harvest is working toward developing a national network of local farms built in fast-growing second cities. The team is bringing farms to Maine and Michigan to serve those communities with fresh produce and career opportunities. In 2024, the Westbrook, Maine facility will have its grand opening, and construction will begin on its Detroit facility. Stay up to date here.
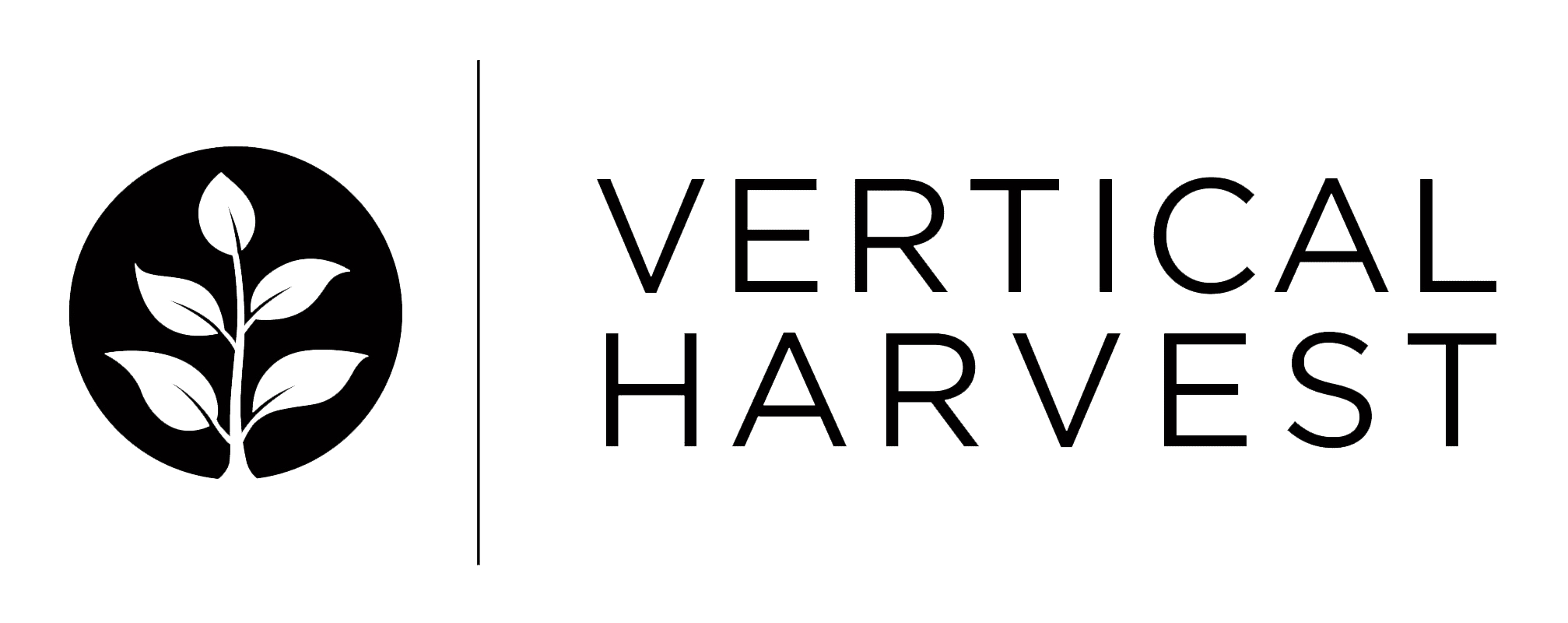
”We prioritize selling 75% of our produce within 150 miles of our farms before we tap into wider distribution networks to ensure food grown here stays here.
Nona YehiaVertical Harvest’s co-founder and CEO
Facility Highlights
![]() | ![]() | ![]() | |
Location | Jackson, WY | Westbrook, ME | Detroit, MI |
Type | Greenhouse with vertical tiers on carousel | Vertical indoor with glazing |
Coming Soon! |
Climate Zone | 7B (Very cold) | 6A (Cold) | |
Crops | Lettuces, Petite Greens, Microgreens, and Tomatoes | Lettuces, Petite Greens, Microgreens, and Herbs | |
Canopy Size (ft²) | 14,429 | 208,281 | |
Lighting | LED | LED |
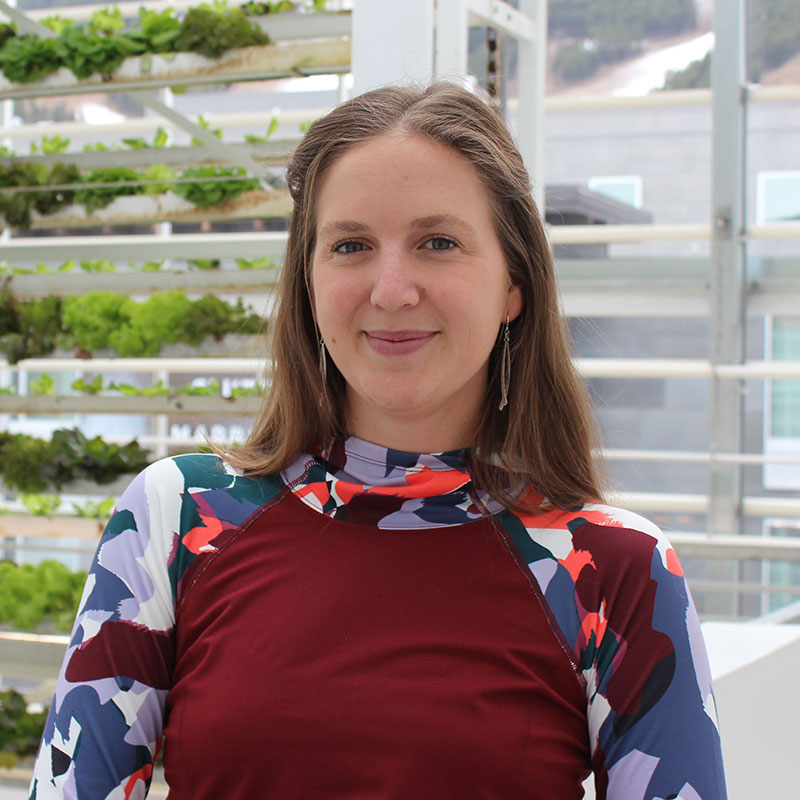
”We are a part of a world-changing industry. Our work will always be evolving, so we want to learn, explore, and innovate as much as we can. This holds especially true for examining resource use and sustainability in CEA - where we are still collectively proving out the case for all of the various production methods to deliver on substantially better environmental outcomes.
Vertical Harvest’s work with the RII Benchmarking program enables us to contribute to the standards and transparency that will allow us to make this case and push our own operations to improve through education and accountability. The facility PREP process has already shaped our approach to metric collection in our Environmental Management System, and we are looking forward to the ways in which PowerScore can help inform our goal setting as others participate in this process.
Hannah BoulineDirector of Impact & Sustainability
Leverage PowerScore
To Establish Benchmarks
The team at Vertical Harvest has used RII’s benchmarking tool, PowerScore, to track sustainability performance benchmarks at its facilities. PowerScore reveals operational key performance indicators of facilities and crops, empowering producers to compare their operations against key performance targets and see year-over-year trends. Aligning with producers’ sustainability objectives, it standardizes resource impacts of energy, water, emissions, and waste to enable data-driven decision-making.
Interested in learning how PowerScore calculates KPIs?
Learn more from our glossary ⟶
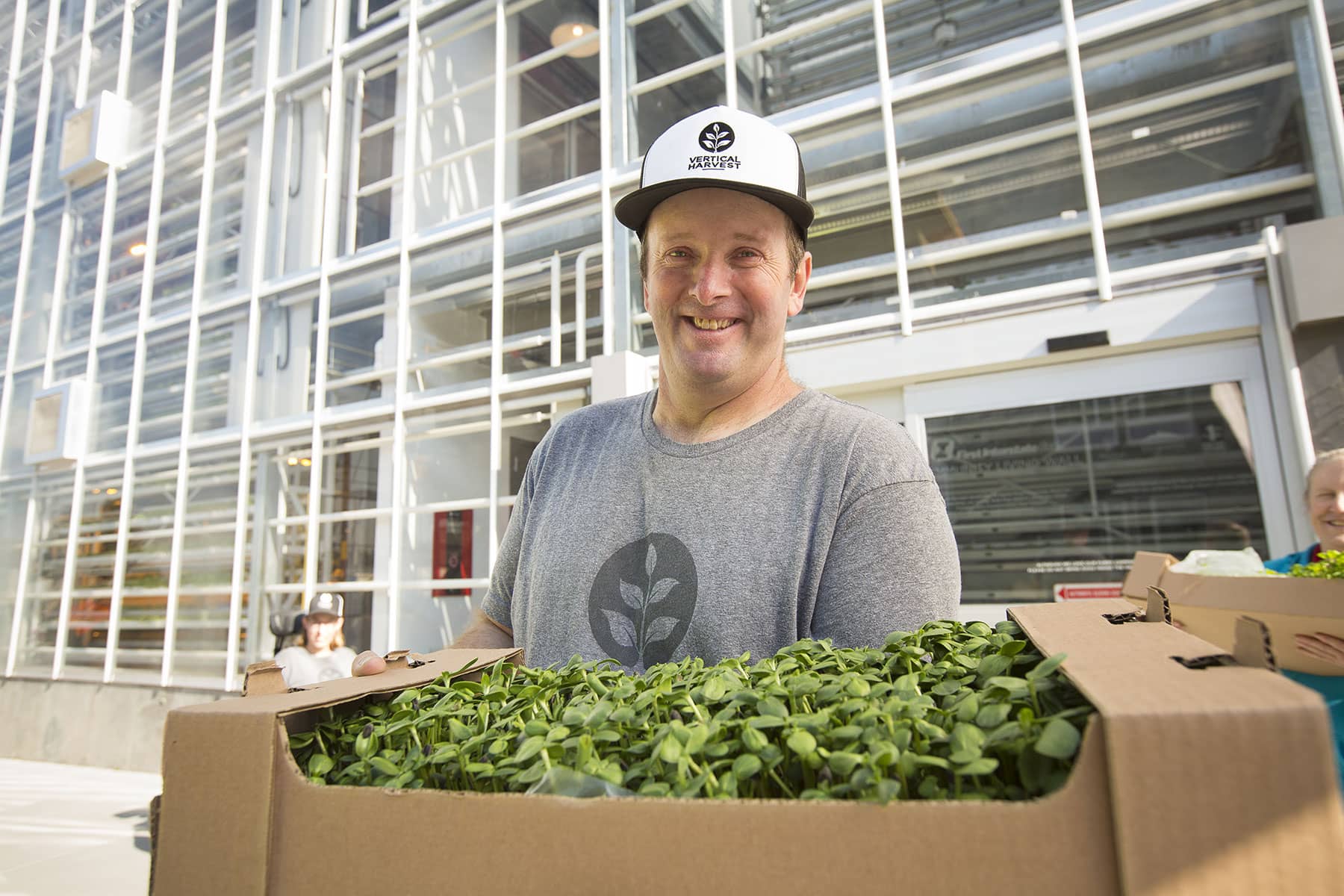
Emissions Reduction
Vertical Harvest overcomes energy challenges through sourcing diversification and emission reduction strategies.
At the flagship facility in Jackson Hole, WY, Vertical Harvest Farms set out to provide fresh produce for its community with minimal environmental impact. This would be no easy feat, as controlled environment agriculture (CEA) can be an energy-intensive endeavor before even considering how Wyoming’s electric grid is one of the dirtiest in the U.S.1
To overcome these key issues, Vertical Harvest took a two-step approach by benchmarking to identify energy reduction opportunities and sourcing renewable energy.
Emissions reduction through benchmarking: Vertical Harvest achieved a 51% reduction in Annual Emissions Productivity from year one to year four.
1 Energy Information Administration (EIA) State Electricity Profiles
* When ranked by greenhouse gas emissions associated with electricity generation
Annual Facility Emissions Productivity of Vertical Harvest Farms
Figure 1 shows the comparison between VHF’s Annual Emissions Productivity, in pounds of CO2 equivalent per pound of sellable product (a lower score means a “cleaner” production). Shown in grey is Vertical Harvest’s Annual Emissions Productivity if it sourced 100% of its energy from Wyoming’s electric and gas grid. Shown in dark green is its actual Annual Emissions Productivity with its renewable fuel mix. Also, shown in light green in this figure is the Annual Emissions Productivity of Vertical Harvest’s entirely electric Maine facility based on projections from R&D in WY.
Emissions are calculated using the total annual emissions associated with energy use of all fuels (converted to lbs CO2e). Learn more from our PowerScore Glossary.
What are energy emissions?
The U.S. EPA defines direct emissions produced by burning fuel for power or heat, through chemical reactions, and from leaks from industrial processes or equipment. Most direct emissions come from consuming fossil fuels for energy.
Interested in learning more about resource tracking and reporting in CEA?
Stay tuned for RII’s upcoming Guide to Environmental Accounting & Reporting for CEA. ⟶
By collecting data on resource use, like annual energy consumption (electric and non-electric), along with crop production, Vertical Harvest established baselines to compare against year-over-year. With these datasets, the team can identify, quantify, and validate energy savings strategies.
“In these buildings that are designed to mimic an ideal growing environment, we have many ways to approach energy reduction and improvement of plant vitality and yield,” Hannah explained. “A primary driver of our energy use and plant yields in our facility is artificial lighting. The horticultural lighting industry has boomed since Vertical Harvest first started production, with LED pricing dropping by 85% and efficiency increasing by 2x. We have upgraded our lighting multiple times over the last 5 years to ensure our plants are receiving the inputs that produce the highest quality produce and best environmental outcomes.”
Emissions reduction through source diversification: Vertical Harvest achieves an average 66% reduction in Annual Emissions Productivity with renewably sourced energy compared to Wyoming’s grid.
Vertical Harvest purchases electricity from The Lower Valley Energy Co-Op, which sources power from The Bonneville Power Administration (BPA) in the Pacific Northwest. The Wyoming facility has an electrical grid mix of over 95% renewable energy sources like hydroelectric and wind.
By using power sourced heavily from renewable energy generation, Vertical Harvest’s Jackson Hole facility improved its Annual Energy Emissions Productivity by an average of 66% over four years. In year four, Vertical Harvest achieved a 72% reduction in Annual Energy Emissions Productivity compared to what it would be if it sourced 100% of its energy from Wyoming’s grid.
Looking to Maine: Vertical Harvest brings the invaluable knowledge learned in Wyoming to the East Coast.
As Vertical Harvest plans for the grand opening of its Maine facility in 2024, the team is taking the lessons learned from Wyoming to inform its emissions reduction goals. The Maine facility will be 100% electric and aims to further reduce emissions as compared to the modeling of average grid-supplied energy in the state through energy purchasing options.
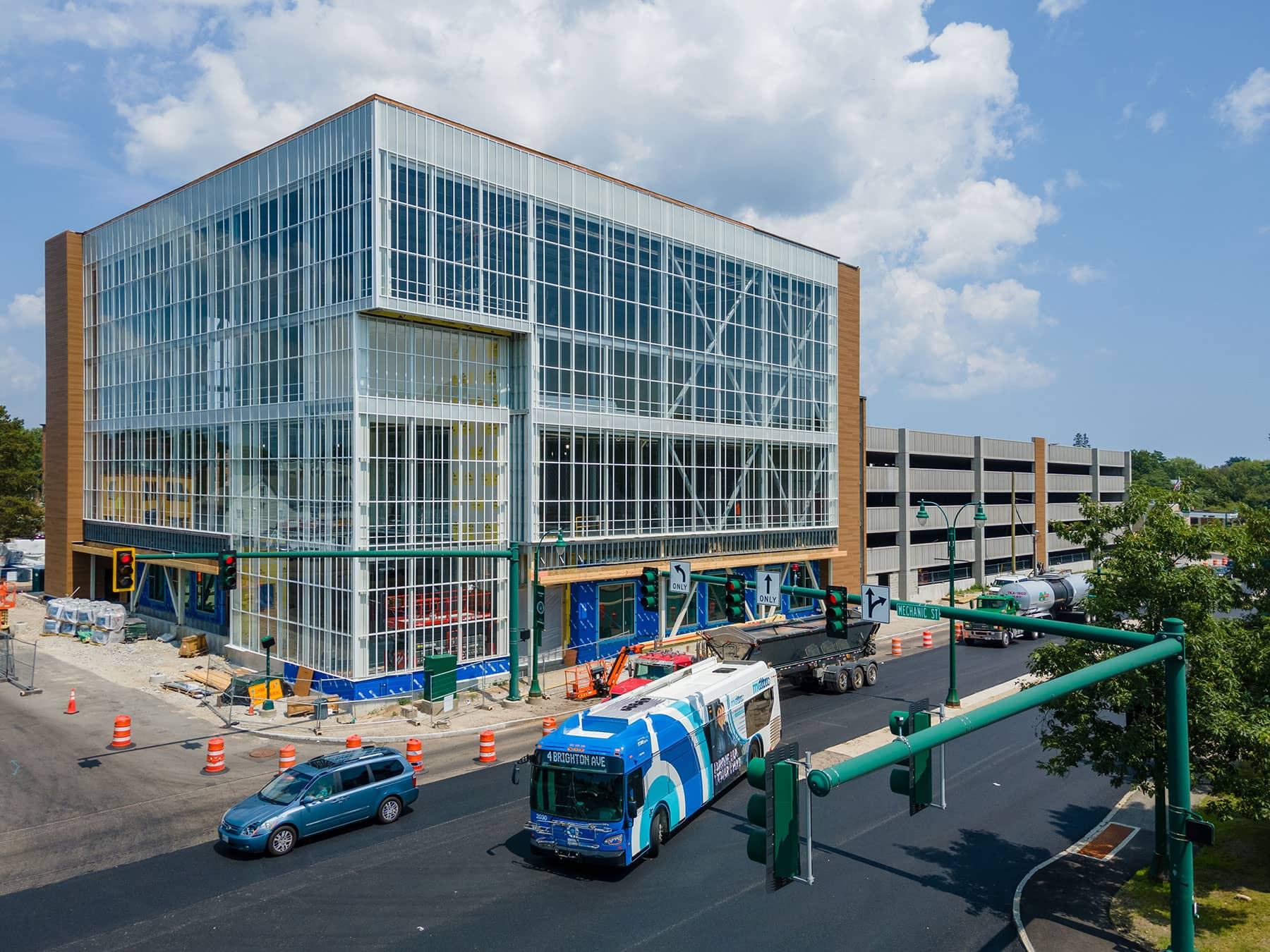
Waste Diversion
Vertical Harvest successfully diverts 95% of its on-site waste from landfills
About 70% of the water humans use globally is consumed by agriculture, and a full third of the greenhouse gas emissions we produce come from food production.2 Despite these massive costs, up to half of the world’s food supply—an estimated 1.3 billion tons—is lost or wasted every year.3 In the United States, between 30%-40% percent of the food supply is estimated to go to waste.4
CEA excels in minimizing food waste by locating cultivation operations closer to consumers. This cuts how far food travels before consumption (known as “food miles”), which minimizes emissions and waste associated with transit.
In Maine, Vertical Harvest will aspire to sell the majority of its produce to the local community, resulting in a farm-to-fridge timeline of less than 48 hours.
Vertical Harvest looked to minimize waste further by tracking the fate of its on-site waste (i.e. landfill, recycling, and compost). In the first year, the team found that only 8% of on-site waste was diverted from landfills to recycling centers. To improve on that, Vertical Harvest developed critical partnerships with other local food producers and helped catalyze local large-scale composting capabilities.
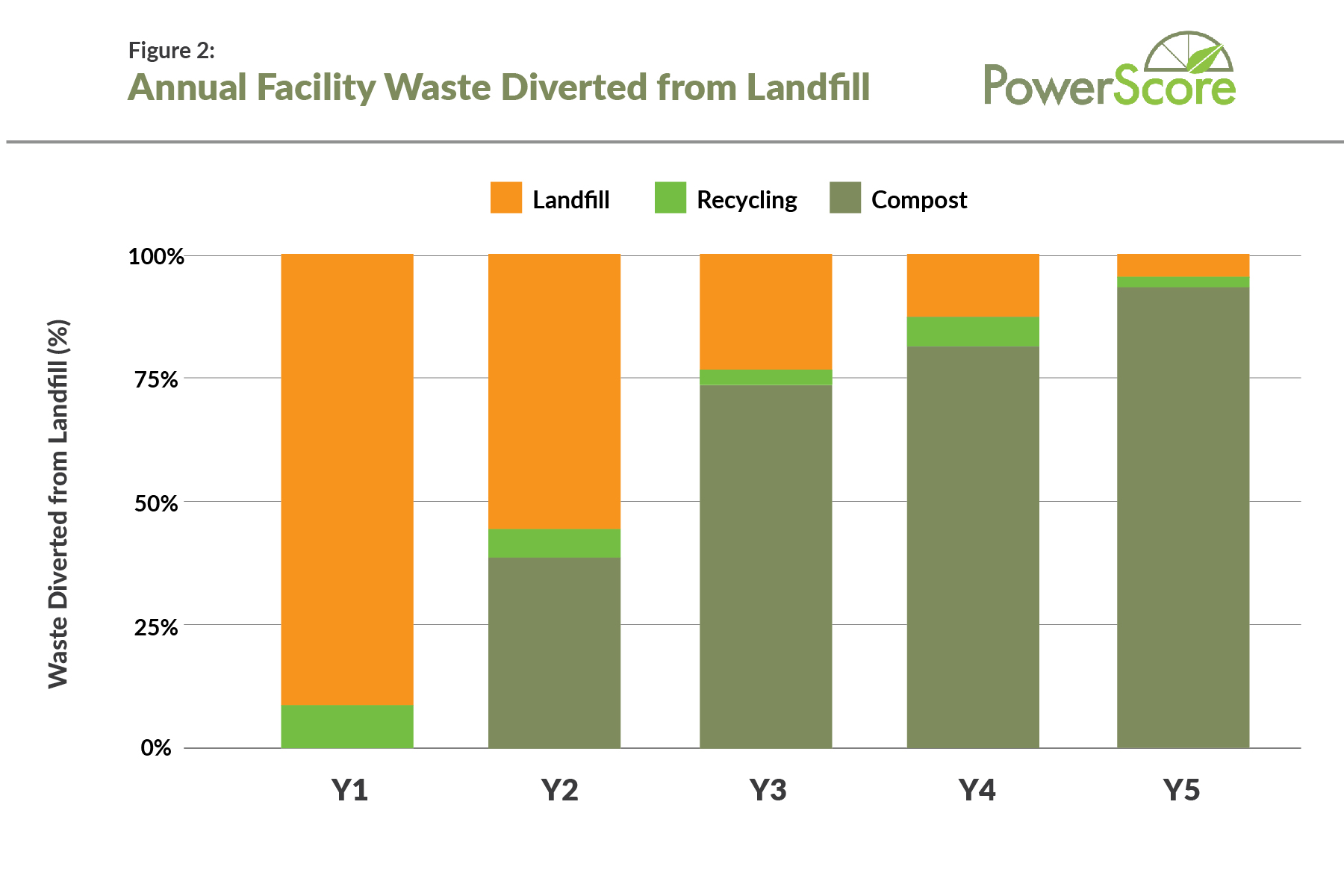
Annual Facility Waste Diverted from Landfill
Figure 2 shows the percent of on-site waste diverted from landfills (orange), or the percentage of total waste (by weight) that is recycled (light green) or composted (dark green) at Vertical Harvest’s Wyoming facility.
Over the next four years, Vertical Harvest has focused on reducing on-site waste, achieving 95% diversion from landfills in its fifth year tracking this metric. As the team prepares for the Maine facility’s opening, Vertical Harvest has identified waste diversion partners and is exploring ways in which it can help create compost infrastructure that serves its facility and community.
Interested in learning ways in which to reduce food waste at the production level?
Check out the USDA’s resource guide. ⟶
Key Takeaways
- By leveraging data tracking platforms (such as PowerScore), significant energy and emissions improvements can be unlocked.
- Massive emissions efficiency reductions can be made by seeking renewable energy sources rather than relying on fossil fuel-supplied grids.
- Tracking waste metrics and developing local partnerships are crucial steps in addressing waste diversion at a CEA operation.
- Lessons learned in state-of-the-art facilities like Vertical Harvest Farms’ Wyoming facility are already being applied to new sites, further increasing the resource efficiency of the entire CEA industry.
Additional Resources
- Interested in learning more about vertical farming? Check out Vertical Harvest’s Top 15 Tips Sheet
- Interested in the latest news from Vertical Harvest? Sign up for the newsletter
- Interested in learning more about the performance of vertical farms through PowerScore? Check out the RII 2023 Energy & Water Benchmarking Report