Building an optimal cultivation environment takes careful consideration of all heat and moisture sources.
Identifying the ideal Heating, Ventilation, and Air Conditioning (HVAC) system size is a critical stride toward resource-efficient Controlled Environment Agriculture (CEA). Cultivating crops in precisely regulated conditions demands a tailored approach, acknowledging factors like crop diversity, facility dimensions, and location nuances.
Here, RII members Adrian Giovenco, CEO at Inspire Transpiration Solutions, and BioTherm Solutions engineers Thad Humphrey (Principal Engineer) and Patrick Wild (Mechanical Engineer) unravel the essential considerations to help CEA facility operators strike the perfect balance between HVAC productivity and sustainability.
Why Sizing Matters
There are production and business drawbacks to both undersizing and oversizing HVAC equipment, all of which can lead to production inefficiencies at best and crop losses at worst.
Undersizing your HVAC system–meaning having a system that is rated to handle a smaller load than your facility’s–is going to make it nearly impossible to meet production targets. Undersized HVAC systems “can’t remove enough energy from the space based on the heat load and based on the amount of moisture that’s being produced by the plants,” Wild explains. “Particularly if you have setpoints that are more aggressive where you’re trying to stress the plant by lowering humidity, you can reach a point where your system can no longer control the environment.”
Not being able to maintain ideal environmental parameters is going to lead to crop quality issues. Undersized HVAC systems can also increase energy use and system wear, as HVAC units will be constantly operating at full capacity as they fight a losing environmental control battle.
“In those scenarios, we advocate for clients to take plants out of the room,” Giovenco says. “If you don’t have more money to buy more systems, take some load out of the space.” While some growers might think this counter-intuitive, by reducing the heat and moisture loads that need to be removed from the cultivation space, “instead of having 30 percent crop loss, [operators] have zero crop loss [by only taking out] 15 percent of [their] plants. At the end of it, they come out far ahead.”
CEA operators wary of undersizing the HVAC system may think that installing a massive unit will allow them to better manage their environment, but oversizing your HVAC system relative to your needs is going to lead to poor outcomes In general, oversized HVAC units will have higher upfront costs, in addition to leading to poor environmental control and higher electrical costs due to “short cycling.”
“Short cycling, when it comes to HVAC equipment, traditionally means that you’re not getting as much dehumidification,” Wild says. “It means you don’t have as much contact time with the coils, which means that you’re not getting as much moisture dried out as you might expect.”
Sizing Factors
Properly sizing an HVAC unit for a CEA operation requires careful attention to the factors influencing heat and humidity loads within the environment. “There’s an art just as much as there’s a science to figuring out what equipment is best for the grow,” Humphrey says.
There are five main variables to have ready when determining HVAC size needs: plant canopy, watering rate, temperature, relative humidity at the lowest rate, and lighting levels. The canopy square footage along with the watering rate and lighting intensity will determine the crop’s transpiration rate. As the number of plants in the space and the lighting intensity increase, more watering and HVAC capacity will likely be required. In addition to having an impact on HVAC system efficiency, temperature and relative humidity setpoints will determine the amount of moisture that needs to be removed.
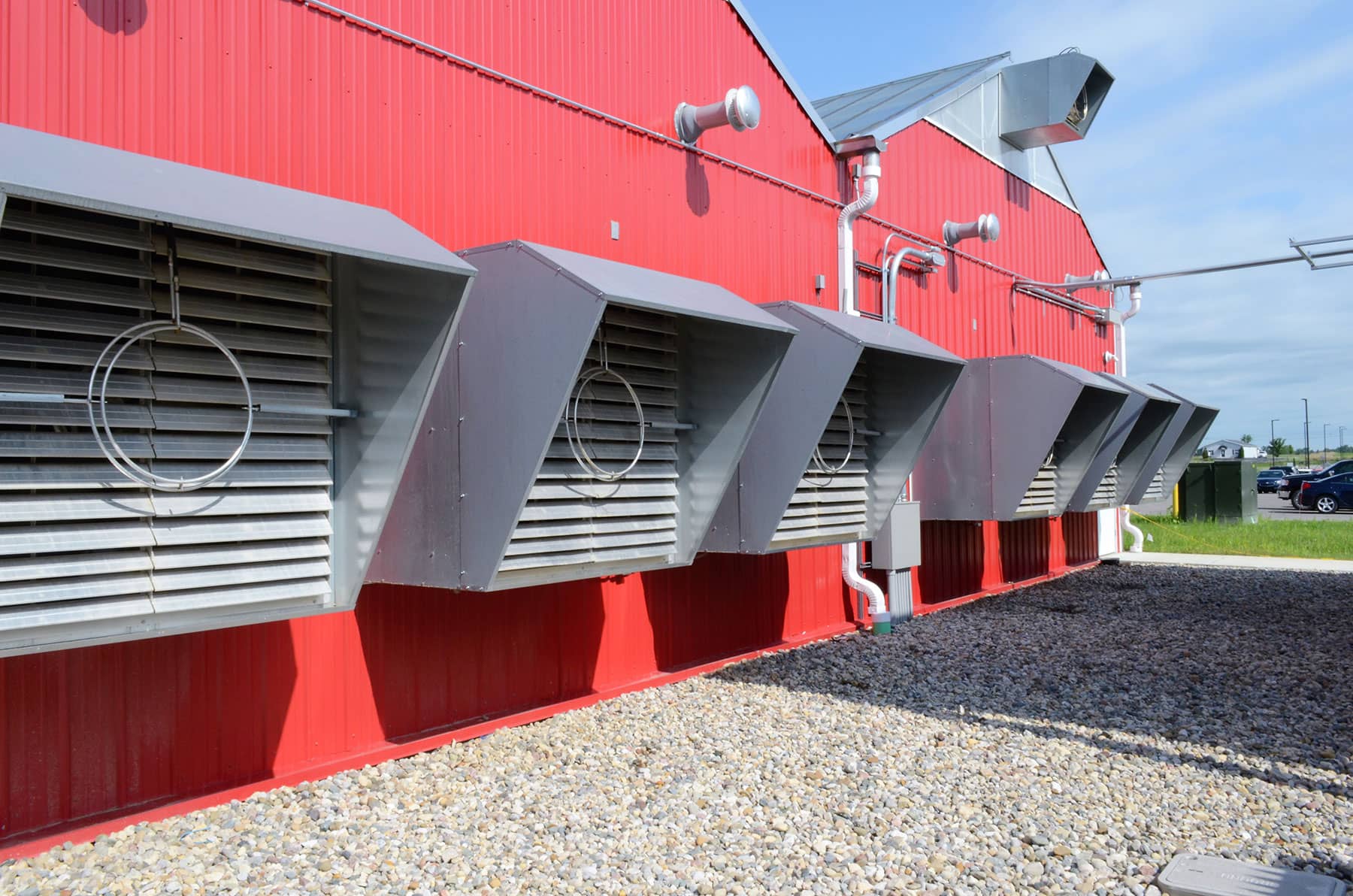
When calculating watering rates, Giovenco notes it’s important to not calculate any fertigation runoff, as this is not moisture that needs to be removed from the environment. “If it goes down the drain, it’s not sitting in the room, that’s not moisture that we need to worry about,” he says. “If these are open top aeroponic or some sort of open vessel setup and there’s going to be evaporation from that water that’s in there… If it’s living soil beds, or there’s other cover crops, then that needs to be considered.”
Temperature and humidity levels can be manipulated to make the HVAC system more efficient. ”In general, warmer air can hold more moisture in it than colder air can,” Giovenco says. “So you’re able to reduce the size of the HVAC system [by targeting] warmer temperatures in the room. Colder temperatures in the room are going to require more capacity to remove the same amount of moisture.”
Lighting intensities have been steadily rising over the last decade thanks to high-efficiency LED fixtures. As growers learn to adapt to these systems, many are noticing the changes that happen to their HVAC’s performance, Giovenco shares, adding that anecdotal evidence points to the relationship between PPFDs and moisture loads being fairly linear.
“If you go from 1,000 PPFD to 1,500 PPFD, you’re going to see a higher transpiration rate, which is more moisture in the air,” he says. Failing to account for that can lead to undersizing issues, leading CEA operators to turn “the lights down to the place where [the moisture load] can be handled, and they’ve just wasted that 20 or 30 percent of money that they just spent on that extra PPFD because they can’t take advantage of it.”
Greenhouse Considerations
If leveraging mechanical cooling for greenhouse or hybrid structures, then local climate and geography “will dictate how much sun you have available and what kind of heat gain you’re seeing at the hottest and coldest parts of the year,” Humphrey says.
Glazing and shade curtains will determine the amount of light and thermal energy entering the space, affecting both the wet and dry energy that need to be managed. Having shade curtains is critical because that is related to the energy that the plant receives from the sun, in turn dictating the crop’s transpiration rate. The less energy that comes into the greenhouse, the less HVAC you have to build in, Wild notes.
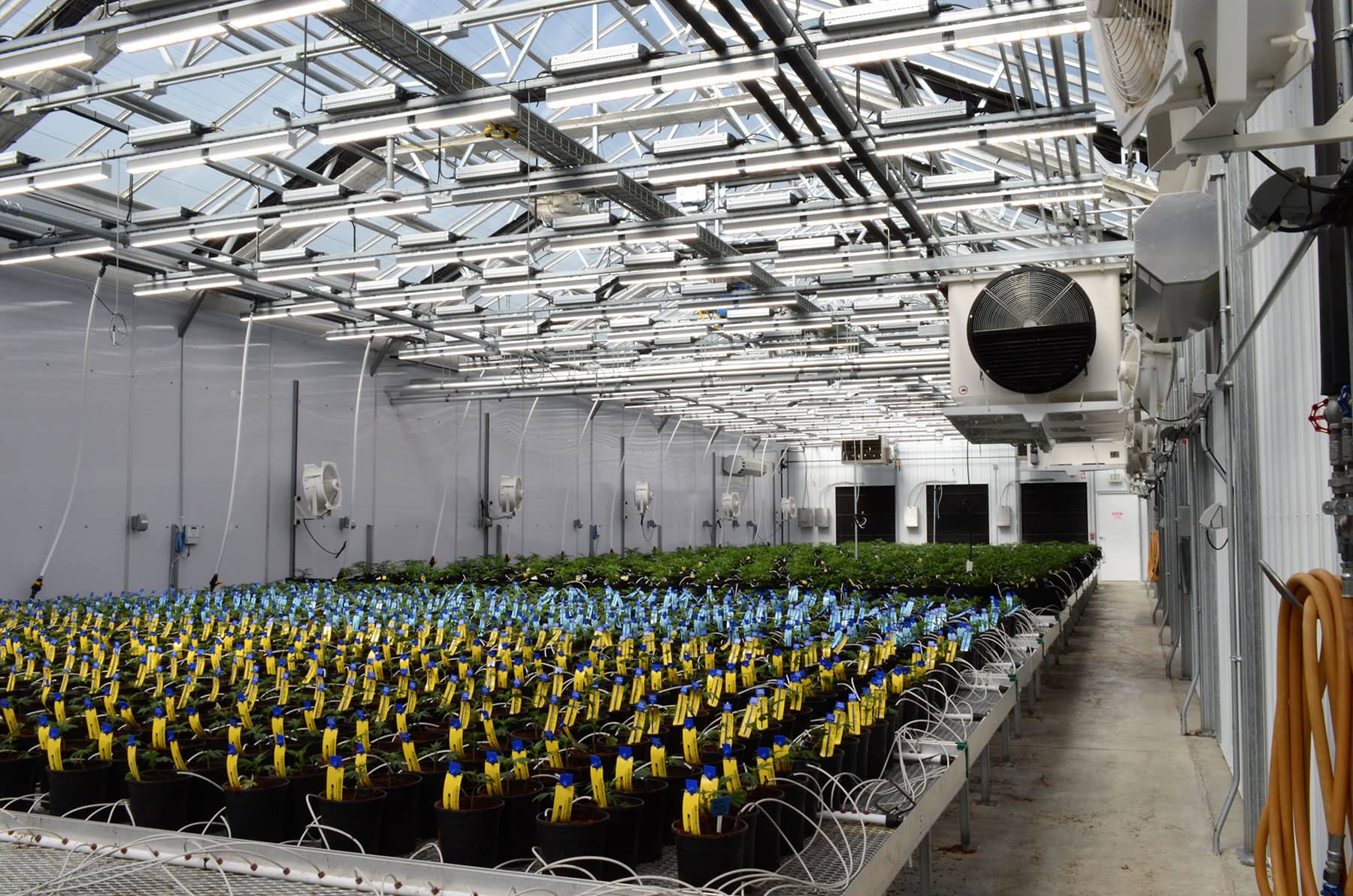
Other HVAC considerations for greenhouse operators include whether they use pad walls and/or ebb-and-flood fertigation systems, both of which will increase the amount of moisture in the air. Additionally, nighttime temperature swings can lead to humidity spikes that need to be removed. “Often, growers will have a set point they like during the day,” Humphrey says. “You could size the equipment to perfectly run at this ratio of sensible heat … [but] that equipment will perform with a different efficiency at night than it will during the day.”
When selecting HVAC equipment, he advises both greenhouse operators and indoor farmers to “select the equipment to handle the worst case of the room, but also check to make sure that it can still function properly at alternate conditions that you want to run the equipment at.”
Determining the right size for an HVAC system is pivotal for optimal CEA production. Mis-sized units can compromise production targets, impact crop quality, and lead to increased energy use. Ultimately, achieving a delicate balance between productivity and sustainability necessitates a thorough understanding of your production inputs and environment.
Meet Our Members
Thank you to our members who participated in this blog. Read more about their organizations below:
Thad Humphrey is a licensed mechanical engineer and Engineering Manager at BioTherm. With over 29 years of mechanical systems design in agricultural, municipal, and mining systems, he has spent the last 13 years providing optimized controlled environment systems to greenhouse growers.
Patrick Wild is a Mechanical Engineer at BioTherm and graduate of Oregon State University who specializes in heating and cooling systems for controlled environments. With a background in lighting, airflow, and Computational Fluid Dynamics (CFD) services, Patrick’s expertise extends to optimizing conditions for sustainability. His senior capstone project focused on evapotranspiration rates of crops, showcasing his commitment to innovative solutions in the field.
Adrian Giovenco is the founder and CEO for InSpire Transpiration Solutions. He has nearly two decades of experience designing, selling, and commissioning HVAC and process control systems throughout North America. Since founding InSpire in 2016, he has focused on deeply understanding the complex and dynamic room balance within indoor cannabis farms and delivering Integrated HVAC&D Systems designed specifically for indoor plant environments.